Anhänger
Alles was du über das Anhängergestell wissen musst
Das Chassis von TechTinyHouse
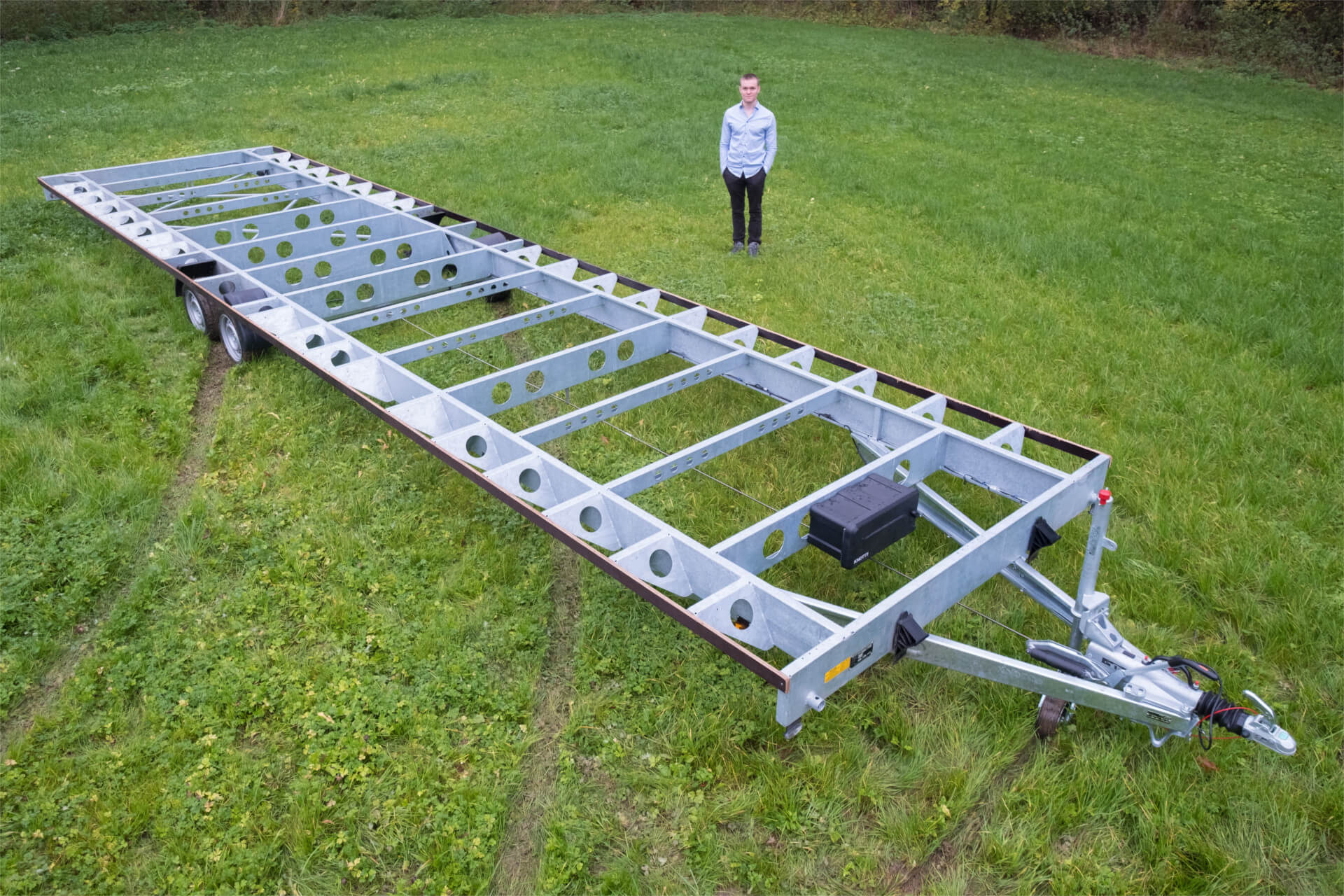
Unser Chassis ist ein wesentlicher Bestandteil unserer ganzheitlichen Systematik im Bau von Tiny Houses
Leichtbau
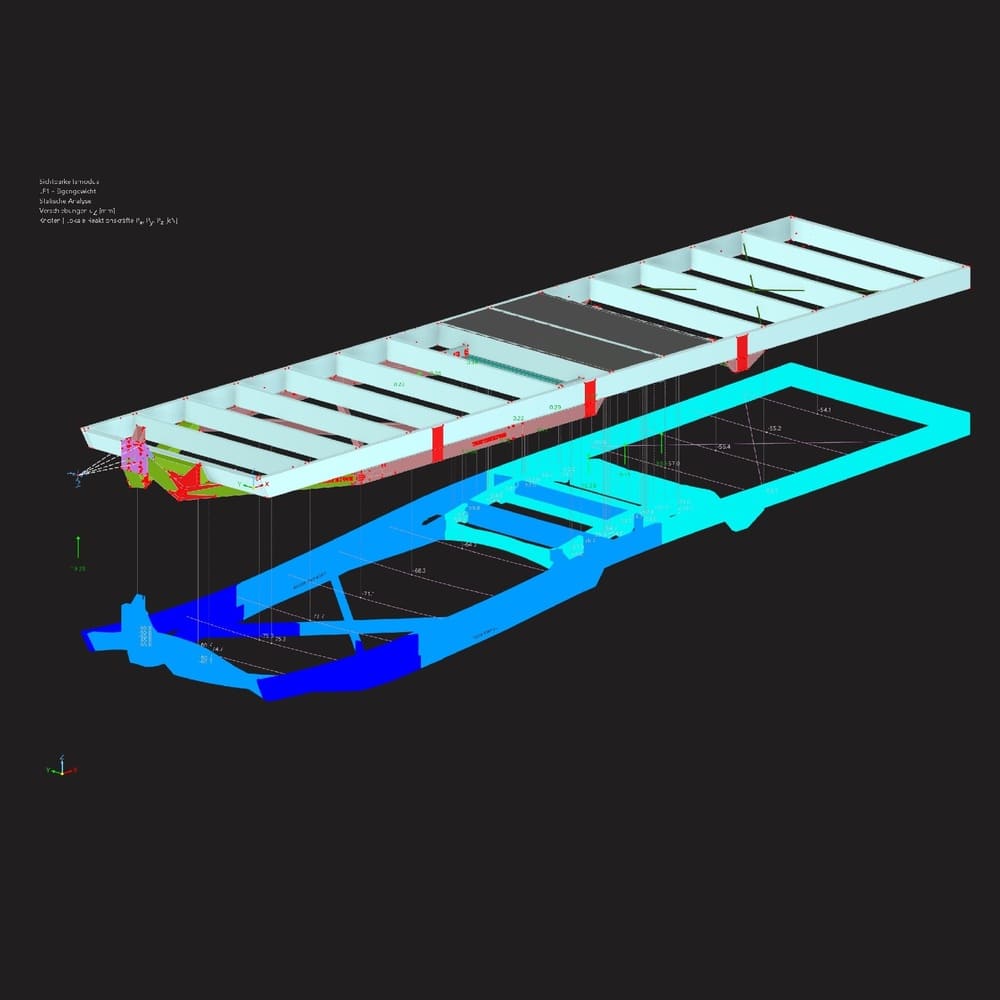
Konstruktiver Leichtbau
Der konstruktive Leichtbau bezeichnet die Gewichtsoptimierung durch Konstruktion. Stell Dir einen Anhänger vor, der mit 500 kg Stahl gebaut ist. Denselben Anhänger hätte man natürlich auch mit 1000 kg Stahl bauen können. Da die Stabilität des Anhängers aber keine 1000 kg erfordert, bauen wir nur mit der Hälfte. Im Umkehrschluss kann man sich genauso vorstellen, durch statische Analysen das Gewicht von 500 kg auf 250 kg zu optimieren. Nämlich, indem wir den Stahl extrem auf Maß schneiden und nur dort einsetzen, wo es gerade benötigt wird. Das ist konstruktiver Leichtbau. Sinnvoll umsetzen kann man diese Art Leichtbau nur mit Unterstützung von Statik-Programmen, die einen davor schützen, an der falschen Stelle zu sparen.
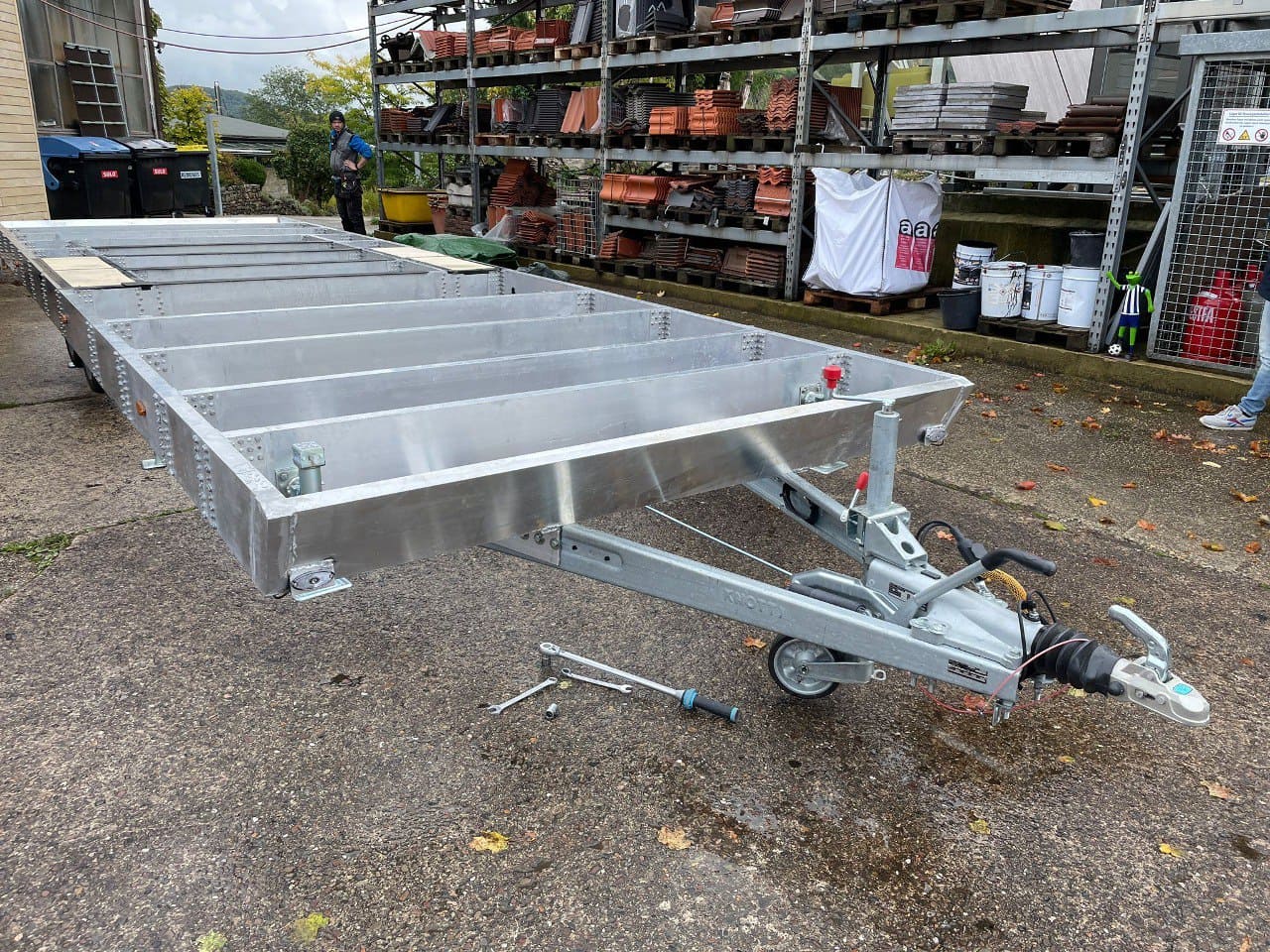
Technologischer Leichtbau
Der technologische Leichtbau umfasst die Gewichtsreduktion durch Technologie. Stell Dir vor einen Anhänger aus Stahl mit einem Gewicht von 500 kg vor. Denselben Anhänger hätte man mit einer anderen Technologie, zum Beispiel dem Material Carbon statt Stahl, mit nur 250 kg bauen können. Das ist technologischer Leichtbau.
Dieses Beispiel ist die einfachste Art von technologischem Leichtbau. Durch die Kombination von Material, etwa bei Komposit-Elementen, ist es möglich, die Stärken einzelner Materialien zu überlagern. In einer Art Kreislauf schützt jedes eine Material mit seiner Stärke die anderen Materialien in ihrer Schwäche. Dadurch wird es möglich, dass das Komposit-Element keine dieser einzelnen Schwächen aufweist.
Material
Stahl
Viele unserer Anhänger fertigen wir aus Stahl. Durch die Homogenität des Materials ist die Formfreiheit groß, und wir müssen bei Löchern und Ähnlichem keine Rücksicht auf Fasern nehmen. Außerdem ist die Bandbreite an Maschinen, mit dem wir dieses Material bearbeiten können, am größten.
Sorte und Güteklasse von Stahl
Es gibt sehr viele Sorten Stahl. Für den konstruktiven Bau sind jedoch nur eine handvoll zugelassen.
Unter diesen die weitaus überwiegenden Anhänger am Markt den Stahl der Güte S235. Aufgrund seiner Häufigkeit und weiten Verbreitung nennt man diesen auch „Feld- und Wiesenstahl“.
Wir nutzen für unsere Chassis eine hochwertigere Güteklasse, nämlich den S355. Der Vorteil ist einfach erklärt: S235-Stahl kann 235 N/mm² (Newton je Quadratmillimeter) an Zugkraft aufnehmen, bevor dieser versagt. S355-Stahl kann 355 N/mm² aufnehmen, bevor er versagt. Unsere Chassis können somit 51 % (355/235≈1,51) mehr Last aufnehmen. Aus Perspektive der Gewichtsersparnis muss ein solches Chassis nur 66 % (235/355≈0,66) bei gleicher Stabilität wiegen.
Diese Güteklasse ermöglicht es uns, anders zu bauen, und verzeiht dem Fahrer möglicherweise manches fehlerhafte Fahrverhalten. Der relativ moderate Preisunterschied ist mehr als gerechtfertigt.
Homogenität
Stahl ist ein homogenes Material. Egal wo der Schnitt erfolgt, ich finde immer dieselbe Oberfläche vor. Damit unterscheidet sich das Verhalten von Metall von dem von inhomogenem Material wie etwa Holz.
Auf diese Weise können wir beim Einbinden von Bohrlöchern, Fügehilfen und ähnlichem unabhängig von der Faserrichtung arbeiten.
Aluminium
Als wesentlich leichteres Material im Vergleich zu Stahl ist Aluminium für Tiny House Chassis sehr interessant. Auch seine Formfreiheit und Bearbeitbarkeit ist sehr gut. Die Korrosionsbeständigkeit ist besser als bei Stahl, nur die Festigkeitswerte liegen bei reinem Aluminium deutlich niedriger.
Sorte und Güteklasse von Aluminium
Doch es gibt Aluminiumlegierungen, deren Festigkeit gut ist und an die von Stahl heranreicht. Wir verwenden die hochfeste Sorte 6082 T6, die obendrein besonders korrosionsbeständig ist. Die Preisdifferenz zu Stahl wird teilweise durch die für diese Legierung nicht notwendige Feuerverzinkung kompensiert. .
Homogenität
Stahl und Aluminium sind homogene Materialien. Egal wo der Schnitt erfolgt, ich finde immer dieselbe Oberfläche vor. Damit unterscheidet sich das Verhalten von Metall von dem von inhomogenem Material wie etwa Holz.
Auf diese Weise können wir beim Einbinden von Bohrlöchern, Fügehilfen und ähnlichem unabhängig von der Faserrichtung arbeiten.
CNC-Bearbeitung
Unsere Stahlteile werden von Maschinen gelasert und von Maschinen gekantet. Durch aufwendig konstruierte Fügehilfen erreichen wir so von Anfang bis Ende gleichbleibende Qualität in Maschinenpräzision.
Fahrt
Ein ordentlicher Anhänger lässt sich selbstverständlich auch gut fahren. Wir beachten deshalb im Design unseres Chassis die geltenden Normen für den öffentlichen Straßenbau. Durch das Verzahnen unserer Stahlteile, die aufwendigen Verbindungen unserer Aluminiumteile, die gewählten Profilgeometrien und zusätzliche Unterstützungen gegen Torsion ist das Fahrverhalten auch bei Chassis bis zu 12 m Länge sehr gut.
Führerschein
Anhänger-Zubehör
Die Achsen, der Zugholm, die Deichsel und andere Kleinteile Deines Anhängers sind auf ein Maximalgewicht von 3,5t ausgerichtet. Das Zubehör für Anhänger >3,5t ist kostenaufwendiger. Insbesondere die Achsen wechseln von einer Gummifederung bei <3,5t auf eine Druckluftfederung bei >3,5t. Für gewöhnlich liegen Letztere beim doppelten bis Vierfachen des Preises.
Hochlader vs. Tieflader
Du findest bei uns aus Überzeugung nur Hochlader: keine den Aufbau und die Raumnutzung störenden Radkästen und keine Begünstigung von Undichtigkeiten und Instabilitäten. Unter ihresgleichen sind unsere Hochlader aber echte Lowrider.
Warum ein Chassis entwickeln?
Bereits nach kurzer Google-Recherche ist klar: Von Anhängern wimmelt es nur so, die Auswahl ist schier grenzenlos. Trotzdem hielten wir es für notwendig, einen Anhänger einzig und allein für Tiny Houses zu entwickeln.
Inverse Lastverteilung
Bei einem Transport werden Anhänger gängigerweise vom Zentrum zum Rand hin belastet. Lade ich beispielsweise Kies oder Schutt auf meinen Anhänger auf, staple ich diesen zur Mitte und nicht zum Rand hin. Befördere ich mein Pferd, steht dieses nicht am äußersten Rand, sondern recht mittig in seiner Kabine.
Auf diesen Lastfall, vom Zentrum zum Rand, sind die Anhänger am Markt typischerweise ausgelegt. Mittelständische Fahrzeugbauer und große Serienhersteller haben die Konstruktion ihrer Anhänger über Jahrzehnte optimieren können. Ihre Konstruktionen sind jedoch auf einen Lastfall hin optimiert, wie er von Tiny Houses nicht generiert wird. Der Aufbau bei Tiny Houses stellt besondere Anforderungen an ihren unterliegenden Anhänger. Diese besondere Anforderung bezeichnen wir als „inverse Lastverteilung“.
Bei der inversen Lastverteilung liegt der Löwenanteil der Last am Rand des Anhängers auf. Je nach Gebäudegröße und Materialwahl macht die Fassade und das Dach bei einem Tiny House 1250-2250 kg aus. Dieses Gewicht liegt einzig auf den äußersten 10 cm des Anhängers auf. Bei einem angenommenen Anhängergewicht von 750 kg bleiben 2750 kg für den Aufbau über. Optimistisch betrachtet liegen damit 45 % (1250/2750), pessimistisch betrachtet 82 % (2250/2750) des Gewichts auf 10 % der Anhängerfläche auf. Diese Anhängerfläche bildet zudem den äußersten Rand des Anhängers, und so muss die Last maximal weit vom Stahl des Anhängers hin zu den Achsen geleitet werden, bis diese an den Erdboden abgetragen werden kann.
Unser Tiny House Chassis ist tragwerkstechnisch optimiert, um eben diese extremen Lastabtragungen zu meistern.
Geometrische Kraftzusammenballung
Die Gravitation stellt eine immer senkrechte Last dar, die wir in der inversen Lastverteilung betrachtet haben. Der Wind wirkt jedoch dominant waagrecht. Diese waagerechten Lasten in Kombination mit der Geometrie von Tiny Houses decken eine weitere entscheidende Schwachstelle traditioneller Anhänger auf.
Die vier Wände eines Tiny Houses bilden stets eine Kastenform. Man kann sich vorstellen, dass die Kraft des Windes von diesem Kasten aufgenommen wird. Diese Kraft wandert in dem Kasten, bis schlussendlich die gesamte Last an den Anhänger abgetragen wird. Diese Abtragung der Windlast erfolgt jedoch nicht gleichmäßig über die Wandfläche verteilt. Während die Kraft in der Wand wandert, wird ein Teil direkt über die Wandfläche an den Anhänger abgetragen. Etwa 50 % ((25 ∗ 4)/(25 × 4 + 15 ∗ 2 + 5 ∗ 7 ∗ 2)) werden jedoch nicht über die Wandfläche, sondern einzig über die Ecken abgetragen. Dies liegt daran, dass die Kraft in der Wand fließt, bis sie an der Ecke nicht mehr weiter wandern kann und vom Eckstiel abgetragen werden muss.
Gehen wir von einem Eckstiel mit dem Querschnitt 10 cm x 10 cm aus, landen so 50 % der Windlast optimistisch betrachtet ca. 2,7 % ((0,1 ∗ 0,1 ∗ 4)/(2,5 ∗ 6)), pessimistisch betrachtet auf ca. 1,5 % ((0,1 ∗ 0,1 ∗ 4)/(2,5 ∗ 10,5)) der Anhängerfläche. Das hört sich krass an, ist jedoch physikalische Realität.
Bis heute ist uns kein Anhänger unter die Augen gekommen, von dem erkennbar ist, dass er diese unverhältnismäßige Lastverteilung bei bspw. einem starken Wind abtragen kann. Im Gegenteil: Die bis dato am meisten für Tiny House genutzten Anhänger sind an den Ecken am schwächsten ausgelegt.
Verstärkungen als Qualitätsmerkmal
Als Verstärkungen bezeichnen wir 2- oder 3-dimensionale Blechkonstruktionen, welche an kritisch belasteten Bereichen des Anhängers verschweißt werden, um das vorliegende Tragwerk zusätzlich zu unterstützen. Hierdurch ist eine Steigerung der Stabilität an dieser Stelle um 100-300 % möglich.
Die Spreu vom Weizen
Grundsätzlich gilt: Einem Tiny House Anhänger, welcher keine expliziten Verstärkungen für Tiny Houses aufweist, sollte man skeptisch gegenübertreten. Denn der Aufbau eines Tiny Houses belastet durch seine Geometrie auf charakteristische Weise bestimmte Bereiche des Anhängers unverhältnismäßig stark. Wir sprechen hierbei von bis zu 17-fachen (34/2) Belastungen an wenigen gezielten Stellen. Es ist wichtig, die Frage zu stellen, warum der jeweilige Anhänger keine Verstärkungen integriert.
Es gibt 3 Möglichkeiten, den Leiterrahmen eines Anhängers zu bauen:
Es sind keine Verstärkungen integriert, dafür jedoch die bereits vorhandenen Stahlprofile „auf den kleinsten gemeinsamen Nenner“ hin stärker dimensioniert. Ein solcher Anhänger würde jedoch mindestens das Doppelte wiegen und kann deshalb nicht sinnvoll als ein für Tiny Houses ausgelegter Anhänger bezeichnet werden, bei dem die Begrenzung auf 3,5t gilt.
Es sind keine Verstärkungen integriert und die Schwachstellen der Stahltraversen werden in Kauf genommen. Auch ein solcher Anhänger kann nicht sinnvoll als Tiny House Anhänger bezeichnet werden, da Gebäude gesetzlich vorgeschriebene Mindestanforderungen an ihr Tragwerk stellen, um Privatpersonen vor körperlichem Schaden und „Ramschware“ zu schützen.
Die Stahltraversen leiten bis zu mittelstarke Lasten eigenständig ab und integrierte Verstärkungen übernehmen besonders kritische Bereiche. Auf diese Weise wird in den Stahltraversen Gewicht gespart und trotzdem die Spitzenlasten entschärft.
Warum Verstärkungen selten zu finden sind
Zum einen ist sicherlich der finanzielle Aufwand ein Faktor, der dazu beiträgt, dass die beworbene Tiny House Spezialisierung der meisten Anhänger sich auf die Namensgebung beschränkt.
Der hauptsächliche Grund ist wohl, dass das Know-how dazu fehlt, was eigentlich Qualität bei einem Tiny House Anhänger bedeutet.
Wir machen dies am Beispiel der Verstärkungen deutlich. Um Verstärkungen sinnvoll zu positionieren, muss ich wissen, wo und in welchem Maße sie am Leiterrahmen benötigt sind. Im besten Fall kann ein erfahrener Anhängerbauer ein gutes Stück Abhilfe verschaffen, indem er typische Sollbruchstellen seiner Anhänger kennt und ihnen entgegenwirkt. Sollbruchstellen sind jedoch stets auf ihren Lastfall hin zu betrachten und der Fahrzeugbauer ist grundsätzlich nicht mit den Lastfällen vertraut, wie sie im Gebäudebau vorliegen. Ein häufiges Argument ist an dieser Stelle, dass Caravans und Bauwagen so unterschiedlich vom Tiny House doch nicht seien und manche Anhängerbauer sich mit diesen Strukturen doch auskennen. Tragwerkstechnisch ist diese Argumentation jedoch nicht korrekt. Denn bei Caravans wird die Last des Aufbaus von den Platten, welche die Wand bilden, in einer Streckenlast auf den Anhänger aufgetragen. Diese Streckenlast ist kategorisch unterschiedlich von der Punktlast, wie sie vom Ständerwerk bei Bauwagen und Tiny Houses in den Anhänger übertragen werden. Ein Anbieter von Bauwagen-Anhängern hat am ehesten das Potenzial dafür, dass sein Verständnis der Sollbruchstellen sich mit denen der Tiny Houses deckt. Anhänger für Bauwagen sind jedoch auf 7,5t und nicht 3,5t Gesamtlast ausgelegt. Zudem macht die meist unterschiedliche Gebäudehöhe, die stärker dimensionierten und häufig komplett andere Profilgeometrie der Stahltraversen, als auch die gegensätzliche Positionierung der Achsen, eine Übertragung der Erfahrung vom Bauwagen zum Tiny House sehr fraglich.
Selbst in einem theoretischen Szenario, in dem ein Anhängerbauer über Trial-and-Error Erfahrung mit den Sollbruchstellen hat, wie sie allein für Tiny Houses charakteristisch sind, kann kein Gebäudestandard erzielt werden. Denn der Gebäudestandard, wie jeder mit einem Dach über dem Kopf ihn tagtäglich unbewusst lebt, fordert mehr als nur die begrenzten praktischen Erfahrungen einer einzelnen Person oder kleinen Gruppe von Menschen. Nach Gebäudestandard zu bauen, bedeutet sich nach den Standards zu richten, wie sie über Jahrzehnte von akademischen Ingenieursgemeinschaften auf Basis empirischer Wissenschaft getragen werden. Eben hierauf basieren die gesetzlich vorgeschriebenen Anforderungen für Gebäude.
Anhängerbauer sind nicht mit Blick auf Gebäudenormen ausgebildet und besitzen nicht die Programme, wie sie für statische Berechnungen in der Bauindustrie notwendig sind, weil sie schlicht nicht der Bauindustrie angehören. Das ist auch in Ordnung so, soll aber nicht zu Verwirrung führen, dass Tiny House Anhänger gewöhnliche Anhänger seien.
Es fehlt allgemeinhin das ingenieurtechnische Know-how normgerechte statische Analysen zu betreiben, die Schwachstellen im Anhänger und damit die Notwendigkeit von Verstärkungen an bestimmten Stellen aufzeigen.
Verstärkungen im Anhängerzubehör
Mit den Verstärkungen im Leiterrahmen des Anhängers ist es nicht getan, denn die Qualität von Anhängerzubehör (Stützrad, Zugholm, Achse) variiert ebenso. Ein Anhängerbauer, der keine Verstärkungen im Stahlrahmen einsetzt, macht sich gängigerweise nicht die Mühe, Verstärkungen im Anhängerzubehör einzubauen. Denn den Anhängerbauer kosten die Verstärkungen im Zubehör mehr als die Verstärkungen im Stahl.
Es ist wichtig Achsen, Stützrad und Zugholm sinnvoll für den Zweck eines Tiny Houses einzukaufen. Diese 3 Komponenten gehören zum Tragwerk, indem sie die Lasten, wie sie vom Ständerwerk eingeleitet werden, aufnehmen und in den Erdboden ableiten.
Wir fertigen einen Wechselbrückenanhänger welcher ein Tiny House als Ganzes auf und abladen kann. Der Anhänger kann so einfach vom Haus getrennt weiter genutzt werden und z.B Zuwasser liefern, Abwasser abtransportieren und Gastanks befüllt wiederbringen.
2024
Die Entwicklung unseres Anhängers
aktuell optimieren wir Planungsunterlagen und Montageprozesse. Entwicklungen am Konzept sehen wir als abgeschlossen.
Durch umfangreiche Recherche, Besuche und Gespräche mit Fahrzeugbauern und Stahlzulieferern wurde ein Leiterrahmen für einen Tiny-House-Anhänger entwickelt. Das Ergebnis ist eine präzise CAD-Datei, die als Grundlage für das Biegen und Lasern des Stahls dient und eine effiziente Beschaffung ermöglicht.
2017
Stahlanhänger mit 3,5 Tonnen Tragfähigkeit und einer Rahmenlänge von 10,5 m, entwickelt in Zusammenarbeit mit einem Fahrzeugbauer. In diesem Projekt stammt der Leiterrahmen aus eigener Planung, während die Beleuchtung und weitere Fahrzeugkomponenten vom Fahrzeugbauer bereitgestellt werden.
2018
Wir setzen weiterhin auf den Bau von Stahlrahmen und optimieren dabei kontinuierlich die Montageprozesse sowie die Abläufe beim Heften und Schweißen.
2019
Der Anhänger wird nun in eigener Werkstatt gefertigt. Nicht nur der Leiterrahmen sondern alle Fahrzeugkomponenten inklusive Leuchten werden nach eigener Planung montiert.
2020
Um den Anforderungen höherer Tonnagen gerecht zu werden, fertigen wir erstmals einen 5,8-Tonnen-Anhänger, der von einem Traktor gezogen wird. Aufgrund der Auflaufbremse ist seine Höchstgeschwindigkeit auf 40 km/h begrenzt.
Im selben Jahr produzieren wir auch einen 5,8-Tonnen-Anhänger mit Druckluftbremse, der nun mit bis zu 80 km/h über die Autobahn gezogen werden kann.
2021
Nach langer Entwicklung fertigen wir den ersten Aluminiumanhänger, beinahe ohne Schweißnähte für 3,5 Tonnen Anhänger. Dieser erlaubt uns mit dem Ständerwerk anders anzubinden und zudem sparen wir zwischen 100 und 200 kg je nach Rahmenlänge. Korrosion und mögliche Zink-Abplatzer gehören der Vergangenheit an.